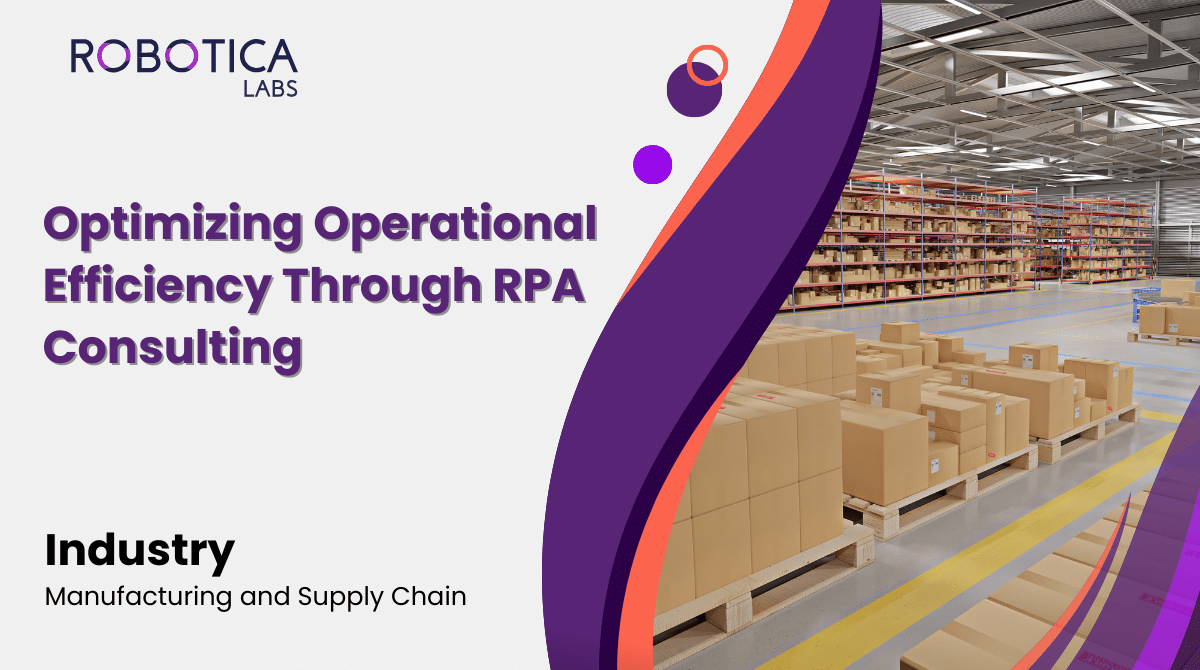
Industry: Manufacturing and Supply Chain
Challenge:
A leading Company in the manufacturing sector, faced operational challenges stemming from manual, time-consuming processes across various departments. The inefficiencies were particularly pronounced in data entry, inventory management, and order processing, leading to increased costs and delayed decision-making.
Objective:
The client sought a transformative solution to streamline operations, reduce costs, and enhance overall efficiency. The decision was made to explore the potential of Robotic Process Automation (RPA) to automate repetitive tasks and optimize critical workflows.
Our Approach:
Comprehensive Process Assessment:
Our team conducted a thorough assessment of company’s existing processes, identifying bottlenecks and opportunities for automation. This involved collaborative workshops with key stakeholders to understand the nuances of their operations.
Tailored RPA Strategy:
Based on the process assessment, we developed a customized RPA strategy aligned with company’s specific business goals. The strategy outlined the implementation roadmap, prioritizing high-impact processes for automation.
Pilot Implementation:
To demonstrate the potential benefits of RPA, we initiated a pilot implementation targeting a critical segment of their order processing system. The pilot allowed company to witness first-hand the efficiency gains and cost savings achievable through automation.
Scalable RPA Integration:
Following the successful pilot, we scaled up the RPA integration to encompass multiple departments, including data entry, inventory management, and order fulfilment. The solution was designed to adapt to the company’s evolving needs and scale with its growth.
Employee Training and Change Management:
Recognizing the importance of employee buy-in, we conducted comprehensive training sessions to equip staff with the skills needed to work alongside automated processes. Change management strategies were implemented to ensure a smooth transition.
Performance Monitoring and Optimization:
Post-implementation, we implemented robust monitoring mechanisms to track the performance of RPA processes. Regular assessments and refinements were made to optimize workflows and ensure sustained efficiency gains.
Results:
Operational Efficiency:
RPA significantly accelerated data entry, inventory management, and order processing, reducing processing times by up to 40%. This allowed company to meet customer demands more promptly.
Cost Savings:
Automation led to a notable reduction in operational costs associated with manual labor, resulting in substantial savings. Company redirected these resources to strategic initiatives and value-added tasks.
Error Reduction:
The accuracy of data entry and order processing improved dramatically, minimizing errors and mitigating the risk of costly mistakes. This bolstered the overall quality of Company’s operations.
Scalability and Adaptability:
The implemented RPA solution proved highly scalable, adapting seamlessly to changes in order volumes and business requirements. This ensured continued efficiency as company expanded its operations.
Employee Empowerment:
Rather than replacing jobs, RPA empowered employees to focus on higher-value tasks that required creativity, critical thinking, and decision-making. Employee satisfaction increased as they embraced their new roles alongside automation.
Conclusion:
Through strategic RPA consulting and implementation, Company transformed its operational landscape, achieving significant efficiency gains and cost savings. The success of this RPA initiative positioned the company as an industry leader in leveraging automation to drive business excellence. As Company continues to grow, the scalable and adaptive nature of the RPA solution ensures continued success and optimization of its manufacturing and supply chain processes.